2011 — “A jacket that makes music when you move; who wouldn’t want to wear THAT!?” An idea that was born at a Kid Koala concert.
MACHINA Founders: A fashion designer, a marketer/trend hunter and an engineer. Our next thought was, how do we do it?
At the very beginning, we where a total of 14 people in MACHINA. We where a group of designers, engineers and developers. We had just raised $50K as a seed investment round from Wayra (an accelerator program from Telefonica Movistar), we felt like millionaires. Our ideas and working methodology was all over the place. The only common factors were our love for design, technology & music.
MJ v1.0 The first jacket that allows the user to create music through motion and touch sensors with a mobile app. Imagine being able to create music by using your body as an interface. Imagine being able to extend that jacket to make it work not only with music, but with whichever devices you have. This was our motto.
The MIDI Jacket allowed to control different aspects of a performance, live act, even music or visual production as any MIDI controller does. The only difference is that this interface is wearable and is mounted on a jacket. We had also designed a set of applications for smarthphones and tablets, Ipad / ipod touch / android. The jacket managed to allow musicians to use a controller that is modular, portable, and with kinetic interaction.
For our first MIDI Controller Jacket prototype we worked closely with Dj’s, Mexican rapper Tino el Pingüino, and b-boy dancers like Funky Maya — to receive their feedback on the jacket, the technology and software itself.
The Jacket — Blue lightweight one layer Gore-Tex fabric bomber jacket with orange flourescent linning with multiple layers to embedded the cables and electronics. Why did we use Gore-Tex? Gore-Tex is considered a Techno-textile. Back in the days it was quite revolutionary and difficult to acquire. For us it was very important to not only revolutionize on the technology part of the garment but also in the kind of fabrics we chose. Techno textiles are fabrics that incorporate new technologies and new functionality into a traditional textile material. Their roots began in industrial and military applications. Techno textiles today are employed in many different applications, ranging across biomedical devices, aircraft, automobiles, electronics, and more, including clothing and home furnishing. Embedding electronic components required water proof fabrics.
The pattern design was carefully crafted many times with a tailor to develop a comfortable effect for the user even though it had cables embedded all through out the jacket. This is why this jacket’s version has raglan sleeves.
Having a cool self drying jacket like Martin McFly’s couldn’t continue to be an idea of science fiction. Design, functionality and high quality materials have always been our priority.
The Technology — Back in 2011 we experimented a lot with open hardware platforms such as Arduino, LilyPad and Flora to make rapid prototyping and really because they where the only devices available to experiment with. At the same time, there was no information regarding wearable technology for the masses and no other people making this as something real. There where several wearable productos out there but they where all focused on working prototypes that where only used as art installations, to dress celebrites for once in a life time ocassions and museums.
On the jacket we mounted a series of soft sensors, three axis accelerometers, a flexible sensor and a 5-button navigation pad, connected to a lilypad card a 3v battery and a bluetooth transmitter.
The lilypad was preloaded with a frame code for serial data transmission. This used to send the values of the sensors as bytes, in such a way that they can be received by a computer or a mobile device preloaded with any of our applications.
All of our work was developed with an open-hardware vision, we are interested in sharing the knowledge that is being generated from this exploration and we needed help from other tinkerers, developers and designers to expand the possibilities of our interface. Up to this day, this remains as part of our philosophy to capture feedback and insights from users and other stakeholders through the open hardware/software philosophy. This allows us to iterate quickly in a relative inexpensive way making it the perfect solution to validate an idea progressively.
2012 — São Paulo, Brazil. The city that changed our lives forever.
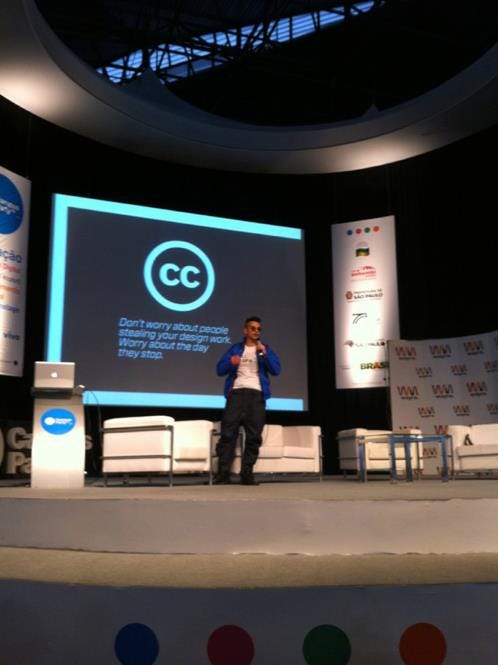
It was spring of 2012, we where invited to give our first live demo and conference at Campus Party Brazil, an annual week-long, 24-hour-a-day technology festival. Thousands of hackers, developers, gamers and geeks equipped with laptops camp out in tents on-site for the conference and hackathon. Antonio, Machina Co-Founder & Creative Director was alone in this journey.
After his presentation, Antonio was approached by a brasilian investor to give once again a private demo of MACHINA’s MIDI Controller Jacket. “This is such an innovative idea, I want someone else to see it.” Five days later, we flew to New York City to meet a millionaire investor who’s investments where mainly focused on fashion and retail.
After making the perfect sales pitch (at least that’s what we thought) we where redirected by this investor to meet a very close friend of his. He gave us the address, didn’t say who it was. Once we arrived to the address, which was located on famous Fifth Avenue, we arrived to what it turned out to be LVMH Moët Hennessy’s headquarters. To our surprise, our meeting was scheduled with LVMH’s Moët Hennessy’s Chairman (back then) responsible for North America: Renaud Dutreil.
“Imagine being able to create music by using your body as an interface. Imagine being able to extend that jacket to make it work not only with music, but with whichever devices you have: A Kinect, an iPod, Nike Plus. We believe that the way we interact with our clothing is changing; clothing should not only be a way of covering your body while helping you get laid, our relationship with clothing should be much more than that: clothing should be an extension of our body, and we’re using wearable technology to do that.” — Machina’s Founders state of mind back in 2012 and what we actually told LVMH’s Chariman.
The first thought that came to mind was visualizing Machina doing a collaboration with LVMH of the bat. The thought alone was worse than a teenagers wet dream. It was an almost two hour meeting full of stammering and an awkward demo of our MIDI Controller Jacket making random sounds when we tried it.
After all, this was his feedback:
- “A jacket that makes music when you move, won’t make it to mainstream markets”
- “You will have to dive into materials and manufacturing to overcome other brands in the market that are starting out like you as well”
- “You have the most beautiful packaging and brand identity I have seen in many years”.
- “Fashion Tech will take YEARS before it hits mainstream. You need to be prepared to be part of the fashion world because it is not easy, I don’t think you know what you are getting into, but if you persevere, I have no doubt you can one day become a success”.
Today Dutreil has gone into consulting but this is a guy who is a Trustee of Museum of Arts and Design, New York City; Member of the Board of New School and of Parsons School of Design. His feedback was not to be taken lightly and it has been something that besides having us inspired; it has followed us to how we deliver our products today.
Our problem with this design overall:
- Gore-Tex although being a techno-textile, wasn’t the best fabric selection. We worked with industrial grade materials which are commonly used for other purposes (boat sails, camping tents),they are completely waterproof and hard to work with. They are not regular clothing materials. Everybody that tested our initial prototype complained of the extreme heat and comfort provided by the jacket. Loved the design, but always ended it up soaking wet in sweat. Not functional for stage performance or long periods of use.
- Having a USB cable from computer to jacket was NOT functional neither modular or aesthetic.
- Using Arduino and LilyPad components wasn’t going to separate us from other designers and engineers trying to build “wearables”. We are a brand and needed to position as such. For that, we decided that if we wanted to be known, we would need to build our own technology from scratch.
2013 — Successfully fundraised $77,002 USD on Kickstarter.
Midi Jacket v1.0 from MACHINA on Vimeo.
The Jacket — One of our main intentions for this MIDI Jacket version was to make all cables “invisible” to the wearers eye. Some of the jackets specs: we added a hoodie for the looks of it, frontal and back had double fabric layers. One being water proof and another with small wholes to absorb the users sweat and make it breathable.
During this jacket’s experimentation we realized that musicians used the accelerometer more than the pad located on the pockets.
The Technology — Our first technology was programmed to be a MIDI controller, but could be adapted to any purpose. (This has always been our mission as a company) We’ve included several sensors so the users can reprogram them.
- Four flexible sensors which can detect your finger’s position
- One accelerometer which can detect your arm’s acceleration
- A joystick
- 4 push buttons
All of these sensors and buttons can be configured by the user, but they come with presets and initial configurations. The sensors are invisible except for placeholders.
This is to make sure that the jacket can be used as a regular jacket. We want integration to be complete, and that’s why we’re working so hard in making sure that, while the sensors are there, they do not affect the look and feel of the jacket. The jacket looks like a regular jacket, and it can be worn under any condition.
We developed this technology from the ground up. The accelerometers make using the jacket a different type of interface for composing music, adding kinetic capabilities. The jacket became a platform. All of our code was available freely, with libraries that extended the functionality of the jacket straightforward.
The Software
We developed a VST plugin so that the jacket can be connected to Ableton live wirelessly. We launched a mobile application for iOS that allowed users to interact with the jacket in a simple way.
- Sound Capturing/Usage
- By recording in the cell phone/Tablet
- Pressing a key and recording a sound
- Configurable pad to match the sensores
- Key Mapping
- Define which keys go with which sounds
- Define which keys add an effect
- Define if the keys are used as buttons, sensors, if they’re pressure sensitive, etc.
-
Define the threshold to trigger actions.
Our problem with this design overall:
- We integrated some sliders on both pockets, replicating a “piano like” function. When working with users, it turned out to be a very confusing function. It was visually unpleasant because it made it look like the wearer was rubbing it’s own body instead of making music.
- Sending left-hand cables to the pad located in the lower right front had to go through many parts of the jacket pattern. What made it very complicated. There was excess cable due to user movements because user movements were abrupt. If there was not enough cable, they ended up breaking the cable. We were forced to rethink the entire product.
- Our technology back then was a big square measuring 20 x 12 cm this turned out to be uncomfortable and created more weight on one side of the jacket.
- The app we developed was designed to control pocket sliders
- Complex and influncial; this made us rethink the design of the app since the sliders in the jacket ceased to exist
- The wireless communication protocol between the jacket with the computer or the ipad was wifi. This made communication very complex due to the lack of development and the high cost of the Wi-Fi module.
2014
MIDI Jacket Demo from MACHINA on Vimeo.
The Jacket — From using several smart techno textiles, we now used improved breathable fabrics on the jackets laterals, waterproof coated.
The jacket’s sleeve was key to this MIDI’s Jacket version. We worked on more than 15 sleeve variations. The sleeve was given a curvature pattern for greater mobility by splitting it in half. A sleeve is usually made out of one piece or two and this was made out of a total of eight pieces — which made it very ergonomic to be in motion including an extra four inches in lengh.
This version included a thumb whole which was key to reach and control the sensors located in the hand. If a tall person was to use our jacket, they would be able to control the jacket easily with this jacket design.
The Technology — KER
KER is a dream all-in-one microcontroller that centralizes a range of functionalities commonly used by wearable technology devices. As such, it offers an HDMI connection to an ITC unit to which you can solder any kind of devices supported by the Arduino platform. Plug any I2C sleeves, pants, props, or wind sensors, LED bars, switches, panels -you name it- and start coding right away.
This board handled communication between your device and the rest of the world by using either an USB cable with serial or MIDI communications (MIDI MocoLUFA based MIDI firmware included in the software downloads), or with the integrated WiFi capabilities, that can run either in infrastructure or ad-hoc mode, offering a wide range of possibilities like serving your performance directly to internet users, so they can use it to keep creating, wherever they are.
Whenever used with a set of ITC and Nervs, you get a complete solution that can be integrated into a hoodie, or a jacket (sounds familiar?), and take it to your exercise routine. Measure your punches, or your slugger swing. If you are a geek, like some of us, go wild using it to remote control vehicles and even robots wirelessly!
The Software — More than generating music, this app’s version was designed to assign what we wanted each sensor to do. We would map notes, sliders or knobs.
Our MIDI Jacket app would let users assign MIDI output channels and save up to four different configurations. In the end the user had three notes per hand and three sliders / knobs per hand, at the same time having one note on the chest. On the chest a note.

Our problem with this design overall:
The idea of creating an open hardware platform became very complex for many reasons.
- We had to develop a custom PCB easy to access by the users, and easy to detach having many ports to eventually connect more sensors to it.
- This became unfunctional because it would put the pcb at risg for mass production.
- Our hardware had a fragil life line due to the fact that it was very easy to get wet if the user didn’t understand it’s proper care.
- Lack of extensive tech support: User communities are out there and can be very responsive, but you really can’t count on the community one hundred percent of the time since it is not their job.
- No one is getting paid for fixing your bugs, provide you or your team the proper training, or respond to your questions and requirements.
Because of all of this and more, we had to remove that board that interconnected our sensors and many others that the users were going to put.

2015- MACHINA’s MIDI CONTROLLER JACKET: A NICHE PRODUCT
99% of the MIDI controllers you’ll find in the marketplace will look like some sort of keyboard. Keyboards are great musical tools; there’s a reason why they’ve been at the center of musical composition for around 500 years.
Our MIDI Controller Jacket wasn’t the product we expected it to be. We did not sell millions of units. It is a very niche product today, limited to people who have a high acquisitive power and deep knowledge of musical instrumentation and experimentation. However, in today’s musical frontier, musicians are breaking free of the shackles of this design convention and looking for new, creative ways to make music — beyond purely tonal sound, and beyond the straightforward performability of single keys representing single notes.
We are no longer alone, there are new ways to generate MIDI being devised every day from startups all over the world. Ideas utilizing wireless Bluetooth, wearable technology, distance and motion tracking, robotics and tactile sensors are revolutionizing the way we can generate streams of data to control sound. With the new MPE (MIDI Polyphonic Expression) protocol recently approved by the MIDI Manufacturers Association (MMA) in January 2018.
Machina x G Shock VS Earth Campaign from MACHINA on Vimeo.
This hasn’t stopped us in collaborating with other companies and musicians from different disciplines. It is a product that has evolved in every aspect from what it first started.
Our latest MIDI Controller Jacket collaboration was with MTV and Koka Nikoladze; sound artist based in Oslo. In the era of software and hardware revolution, Koka makes a standout as a modern musician, maker and hacker.
By 2015, it was already five years of continuous research, prototyping and development with high complexity in every part of the product having no luck in scalability. A product that we thought that everybody would love turned out to be completely the opposite. We felt lost in a very much need to reebot.
We began making internal and open to public hackathons. The objective was simple, we wanted to really understand why did we fail, what could we change to make things better and how could we expand a five year investment.
Back in 2015, VR short for Virtual Reality was having a crucial and significant hype thanks to Oculus Rift which was acquired for $2billion USD by Facebook.
After sleepless and cold-less nights with cheese filled croissants combined with candy and terrible cold coffee we knew that to continue in following our vision of functional, modular garments, we needed to redesign our technology and intergration process. That’s when we killed KER,The MIDI Controller Jacket and designed OBE (Out of Body Experience).

2016 — From music to VR & more! OBE (Out of Body Experience) — a family of four controllers and sensors that are completely modular, functional and easy to use. A groundbreaking technology that enhances and expands human capabilities.
A new technology development which required new and deep understandment of market wants and needs. Further investigation and iteration on the integration process of electronic components into clothing.
To fulfill our vision of having a totally user friendly and functional product we partnered with key players that would help us grow and take our company to the next level. ASTRO Studios: design firm responsible for many of the world’s most recognizable tech and lifestyle products, including the Nike Fuelband and Microsoft’s Xbox 360. Ranked 6th on the design sector for Fast Company’s list of “The World’s Most Innovative Companies” for 2018.
We did an intensive six month research and development process with rapid prototyping hand by hand with ASTRO Studios. Our main focus during this period was the one and only mechanical engineering aspect and look and feel of the technology. We no longer wanted people to feel intimidated by such “high-tech product”. It was very important for us to continue on having a strong design and functionality focus. Through out the process, we where relying on ASTRO’s experience for end user product experience.
OBE is fashionable and completely intuitive to the final user. It captures the user’s movements translating them into 3D data, creating a physical immersive experience.
A truly open wearable technology platform designed for videogames (on mobile, consoles and PC), flying drones, controlling lights, and most proudly — making music using it as a wearable MIDI Controller. This is the evolution of our MIDI Controller Jacket on steroids. Completely revolutionaized.
Because of it’s modularity, OBE tech allows you to use four sensors for a complete immersive experience with our haptic feedback and motion features there is no limit. You can adapt the sensors and controller from four to more than 15.
It took us three years to design and develop a family of four electronic components that could be completely embedded into our garments. These four electronic components today, are a fundamental part to any of our garments.
We’re suiting up tech savvy humans , people who want to take our clothing into the unknown. Pushing the technical process in both construction and function of clothing to define fashion through techwear.
We divided OBE Tech into two lines of products:
- E.X.O.M. (Extension. of. Myself) — captures users body movements, has all controller functions providing a full immersive physical feedback (full body mesh vibration) and provides unique gamer biometrics back to the game, to create adaptive gaming for a full emotional immersion. Our wearable technology and fashion team, designed a unique jersey using OBE technology inside, that covers all consumer needs and brings a new level to gaming. Competition is yet only in gesture control or limited immersion. We call this full immersive experience E.X.O.M. (Extension of Myself) . This will be a very programmable kind of product and used more for different kinds of experiments beyond VR; like controlling lights, video, etc.
- E.S.P. (Extra. Sensory. Perception) — Our mainstream line of products that contain only one sensor today compatible with 26 different garments. Engineered for complete and functional mobility. Integrating thoughtful design details for active use in any modern city. Groundbreaking garments, with OBE Technology inside that link to your mobile device via Bluetooth. With a simple tap you can control music, lights, receive smart notifications, create a panic button and more! A few simple gestures pump up your multitasking skills, keep you in touch, and connected. Smart clothing for today’s modern world. All of our E.S.P. products are now available worldwide and in specialized retailers.
It’s 2019- after 72 different prototypes varying from the beginning of the MIDI Controller Jacket to the evolution of OBE Tech — open hardware in clothing is not viable.
Designing an app or specific interface is not profitable if it is not simple or easy to use for end user. An app is considered successful if the app is being opened at least once a day by the user. We had to learn the hard way on the importance of design and developing a user friendly application.
“No product is an island. A product is more than the product. It is a cohesive, integrated set of experiences. Think through all of the stages of a product or service — from initial intentions through final reflections, from first usage to help, service, and maintenance. Make them all work together seamlessly.”
— Don Norman, inventor of the term “User Experience”
Overall, building a garment can be as complex as building a robot. Clothes with embedded technology require specific machinery and access to materials. To scale technology components is something that needs to be thought about from the very beginning. Garments ergonomics is key for a functional end product.
‘Wearable Technology’ has as one of its main implications the possibility of integrating clothes into life as an extension of oneself, dissolving in some way the limits that distinguish between [humans] and [machines].
Creating — and the risk that this entails — is from the beginning a prevailing in the work of MACHINA. We emerged as a [project] — [prototype] thesis that after a first rejection became a device in constant change that eight years after its inception raises a series of questions about what the future holds as a meeting point between design, technology, sustainability, consumption, transit and fashion.
As founders, we are constantly motivated by the idea of extending the life of our products by providing our community a fun, functional and easy to use interaction with their garment. This has gone beyond wearing and every day to day kind of jacket. This is a complete amplification of human’s identity and interation with it’s surroundings. This is the forefront of the human-machine relationship: human + clothing.
This is not an end to our MIDI Controller Jacket. There has been a rebirth. We will continue to re-invent how we interact with fabrics, clothing and technology.
FIND ALL OF OUR AVAILABLE PRODUCTS HERE — NOW AVAILABLE